Why Rotational Molding is the Best Choice for Complex Plastic Designs
Why Rotational Molding is the Best Choice for Complex Plastic Designs
Blog Article
Rotomolding, short for rotational molding, has become a game-changer in the production earth, especially in regards to making top quality, resilient plastic products. This versatile process is employed to design from industrial equipment to client goods, giving unparalleled toughness and style flexibility. Over the years, advancements in Rotomolding have led to more revolutionary alternatives, rendering it an essential process for producing plastic products and services that withstand the test of time and hard conditions.
What's Rotomolding?
Rotomolding is an activity that requires heat plastic resin inside a mold, turning it in multiple axes, and letting the product to stay in to the specified shape. That effects in a hollow part that is uniform, strong, and lightweight. The method it self is very successful, providing companies with the capacity to create complex and complicated designs which can be both cost-effective and robust.
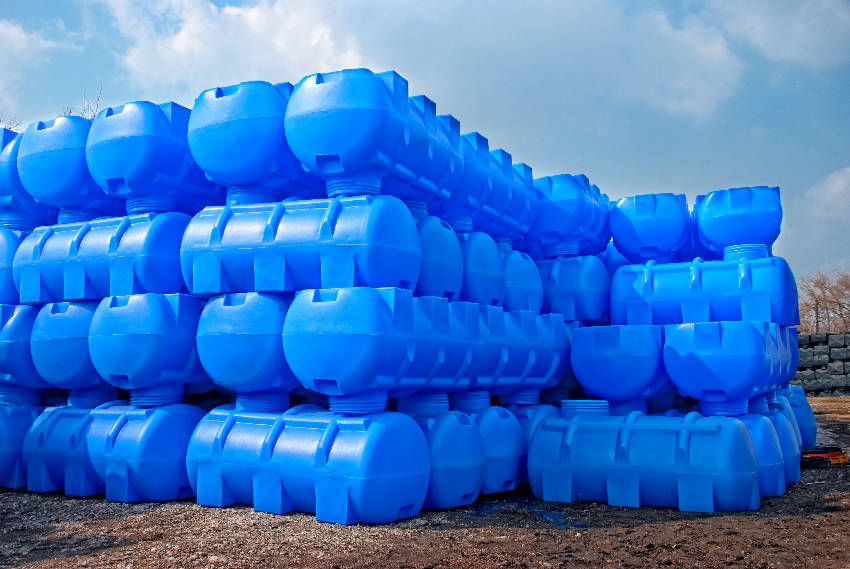
Critical Advantages of Rotomolding
Among the primary reasons for the growing recognition of rotomolding is their ability to produce products and services which can be tolerant to use and tear. Unlike other plastic manufacturing practices, such as for instance injection molding, rotomolding may generate seamless services and products without any bones, which somewhat reduces the likelihood of weak points wherever breaks and problems may form. That easy design makes rotomolded services and products well suited for outside and high-impact applications, including storage tanks, playground equipment, and maritime products.
The procedure also allows for freedom in product design. Whether it's a product with various wall thicknesses, unique color needs, or custom designs, rotomolding afford them the ability to create correctly what's needed. This mobility implies that businesses can force the limits of design, creating products that match specific useful and aesthetic requirements.
Sustainability and Performance
Along with its toughness, rotomolding offers substantial environmental benefits. The procedure creates minimal spend in comparison to different manufacturing techniques, as any outstanding plastic may frequently be reused in future manufacturing cycles. This, combined with energy-efficient nature of rotomolding, helps it be a sustainable selection for makers seeking to reduce their environmental impact.

Moreover, rotomolding produces products quicker and at a lower cost than a great many other methods. The paid down need for labor-intensive assembly and the capacity to build complicated designs within a stage decreases overall generation expenses and reduces the time necessary for development. That effectiveness makes rotomolding a stylish choice for industries including automotive to customer goods.
Conclusion
Rotomolding is revolutionizing the entire world of plastic production, giving impressive options for producing tough, tough, and sustainable products. Their power to create high-quality, complex designs with minimal waste and price has managed to get a favored process in many industries. As technology continues to evolve, the prospect of rotomolding to create also more advanced and functional products will only improve, driving development and creativity in a variety of sectors. Whether for professional or everyday purposes, rotomolding is shaping the future of plastic solution style with resilience and ingenuity.
Report this page