Rotational Molding: The Key to Durable & Impact-Resistant Plastics
Rotational Molding: The Key to Durable & Impact-Resistant Plastics
Blog Article
Rotomolding, also referred to as rotational molding, is an progressive manufacturing process that provides a very cost-effective alternative for producing supreme quality plastic products. That versatile approach has obtained significant acceptance lately because of its power to create resilient, lightweight, and delicately developed plastic items. Whether for professional, commercial, or consumer use, Rotomolding is really a preferred choice for many industries searching for trusted and inexpensive production solutions.
How Rotomolding Performs
The procedure of rotomolding involves the utilization of a form that is spun on numerous axes while plastic dust or resin is heated within the mold. While the substance is hot and melted, it evenly coats the inner areas of the mold. The shape is then cooled, solidifying the plastic into its ultimate shape. This unique method enables the production of hollow elements, complex patterns, and uniform thicknesses that would be hard or impossible to attain with other molding techniques.
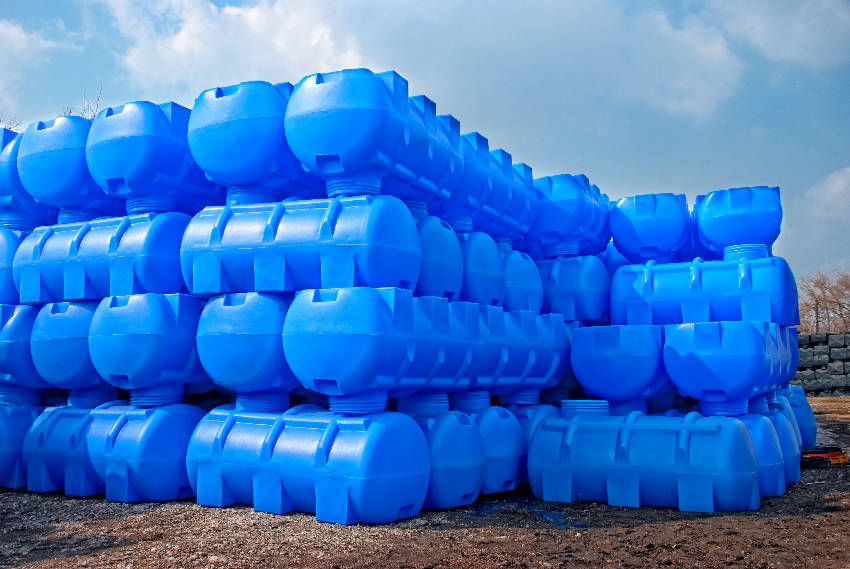
Important Benefits of Rotomolding
Cost-Effective Generation: Rotomolding is one of the most affordable plastic production methods, specially when making moderate to big quantities. The molds used in rotomolding are usually more affordable than procedure conforms or hit conforms, rendering it a nice-looking choice for organizations looking to help keep fees low.
Versatility in Design: This technique allows manufacturers to create a wide range of forms, styles, and types, which makes it well suited for programs that need custom or unique products. The flexibility in design also guarantees that companies can create items with various wall thicknesses, which contributes to the durability and performance of the completed product.
Durability and Power: The plastic areas produced through rotomolding are known for their strength and weight to influence, creating them ideal for outside and heavy-duty applications. Also, the process guarantees even distribution of product, which effects in products and services with standard thickness and increased durability.
Environmental Sustainability: Rotomolding is also an green process. As it uses fairly reduced amounts of power and yields little spend, it helps minimize the environmental footprint connected with manufacturing. Several businesses are now prioritizing eco-friendly manufacturing processes, and rotomolding meets seamlessly in to these sustainability goals.

Applications of Rotomolding
Rotomolding is utilized in a wide selection of industries, from automotive to agriculture, and actually games and recreational products. It's frequently applied to produce big objects such as for example storage tanks, watercraft, and playground equipment, in addition to smaller, delicate parts like areas for medical devices. The versatility of rotomolding helps it be a go-to option for industries looking to innovate with plastic products.
Conclusion
Rotomolding has an efficient, cost-effective, and flexible strategy for providing supreme quality plastic products. Using its capacity to create complicated forms, longevity, and minimal production fees, it's no surprise that so several industries are turning to this process for his or her production needs. As need for high-performance plastic products is growing, rotomolding is set to enjoy an significantly important role in shaping the continuing future of plastic manufacturing.
Report this page